Manufacturing operations demand reliable, real-time communication to keep teams aligned and to enable safety across the board. Motorola’s advanced communication ecosystem provides an integrated solution that overcomes the challenges of connecting teams across various devices and locations.
By leveraging innovative tools like WAVE PTX, manufacturers can experience flawless coordination, improved safety, and greater productivity. This article explores how Motorola’s system can completely change—for the better—the way teams communicate.
The Role of Communication in Manufacturing
The role of communication is pretty clear in many industries. In healthcare, quick and reliable communication can mean the difference between life and death. In public safety, law enforcement relies on fast communication to keep us safe. In entertainment venues, security personnel rely on communication to share potentially dangerous or suspect situations to others who need to know.
What about manufacturing? How is communication so important, and why is a unified system of such great benefit? Well, in manufacturing, production lines, maintenance crews, and management teams often work simultaneously but from different areas of a facility or even across multiple locations. Delays in communication can lead to production downtime, safety risks, and missed opportunities.
Manufacturing environments face unique communication challenges. Staying connected can be difficult, with multiple teams that often spread out across large areas. Each department may rely on different tools or networks, which can cause gaps in communication and make live collaboration difficult. These disconnections can lead to slower response times, unclear instructions, and even unsafe working conditions.
Traditional communication tools, like two-way radios, often need more flexibility in a high-demand setting. These tools may need more coverage, especially in large or multi-site facilities, and signal reliability can be inconsistent, particularly in areas with physical obstructions or environmental interference. Additionally, many legacy systems aren’t equipped to handle modern communication needs such as file sharing, video transmission, or precise location tracking.
This is where a unified communication system can completely change the game. Bringing every team member, device, and department onto a single platform helps bridge these gaps, allowing for flawless and highly reliable coordination and better-informed decision-making.
Introducing Motorola’s Advanced Communication Ecosystem
We teased it out earlier, but without further ado, let’s talk about Motorola’s advanced communication ecosystem and why it matters for your manufacturing operations. At the heart of this ecosystem is WAVE PTX, a powerful platform that allows real-time communication across all devices and locations. Whether your team members use smartphones, tablets, or two-way radios, WAVE PTX connects everyone.
One of the most popular features is the push-to-talk across devices, which turns any smartphone, tablet, or desktop into a walkie-talkie. With a simple tap, teams can exchange information instantly, breaking down the barriers between departments and locations. Whether it’s a production update, an urgent alert, or a routine check-in, communication flows without fail and keeps everyone aligned.
Scalability is another key feature of this ecosystem. Whether you’re running a small facility or managing a large multi-site operation, WAVE PTX grows with your business. The cloud-based deployment means no need for major infrastructure investment upfront, and you can scale communication capabilities as your needs evolve.
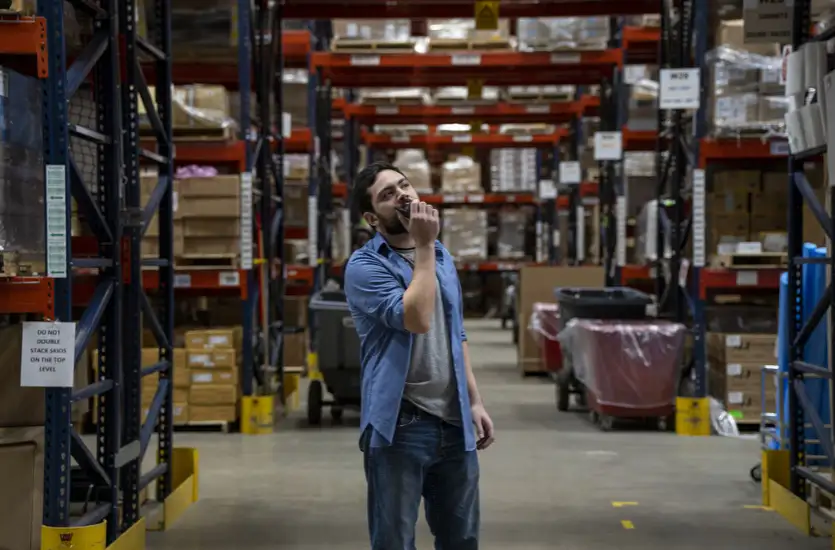
Key Benefits of Motorola’s Communication Ecosystem for Manufacturing
Sounds too good to be true, right? After all, what organization wouldn’t want a system that could integrate with the devices they have on-site? We promise not only is it not too good to be true, but you can benefit from this evolved ecosystem now.
Here’s what you can expect.
1. Improved Safety in Manufacturing Environments
WAVE PTX increases safety by offering real-time emergency alerts, location tracking, and secure messaging, all of which help teams respond quickly to potential risks or incidents. For example, in an emergency, workers can send instant alerts to supervisors and response teams, enabling immediate action.
Location services allow managers to monitor team members’ exact positions, even in remote or high-risk areas, which is crucial in large manufacturing facilities. In one case study, a mining operation successfully used Motorola’s system to track workers and reduce the chance of accidents.
2. Better Operational Efficiency
WAVE PTX enables manufacturing teams to communicate without fail, reducing downtime and allowing for faster decision-making. By providing real-time connectivity between operators, managers, and technicians, WAVE PTX makes it possible to resolve issues as soon as they arise.
For example, technicians can be immediately informed and dispatched to address the problem if an equipment malfunction occurs, minimizing delays. The ability to communicate across devices and locations means that whether employees are on the factory floor or off-site, they remain part of the conversation.
3. Unmatched Interoperability
One of the greatest advantages of Motorola’s communication ecosystem is its ability to integrate different devices into a single platform. In manufacturing, various teams often rely on different tools, from radios to smartphones, which can create communication gaps.
WAVE PTX eliminates these barriers by providing interaction across all devices. Everyone from machine operators to office staff can communicate instantly. This kind of integration grows overall efficiency by keeping everyone on the same page.
Motorola’s Push-to-Anything Functionality
We already discussed Motorola’s push-to-talk across devices capability, so now let’s take a look at the push-to-anything capability that comes with WAVE PTX. This functionality simply strengthens the game.
Push-to-anything allows team to instantly share critical data, such as images, videos, and documents, making communication so much more comprehensive. This capability is especially valuable where visual information can be a must for resolving issues or providing updates. For example, a technician can send a photo of a malfunctioning machine part to the engineering team for quick analysis, allowing them to troubleshoot or prepare for repairs without delays.
This expanded communication tool leads to faster, more informed decision-making. By sharing real-time images, videos, or documents, teams can respond to challenges with the right information at their fingertips. This functionality means reduced miscommunication and lets the team take immediate action based on concrete data.
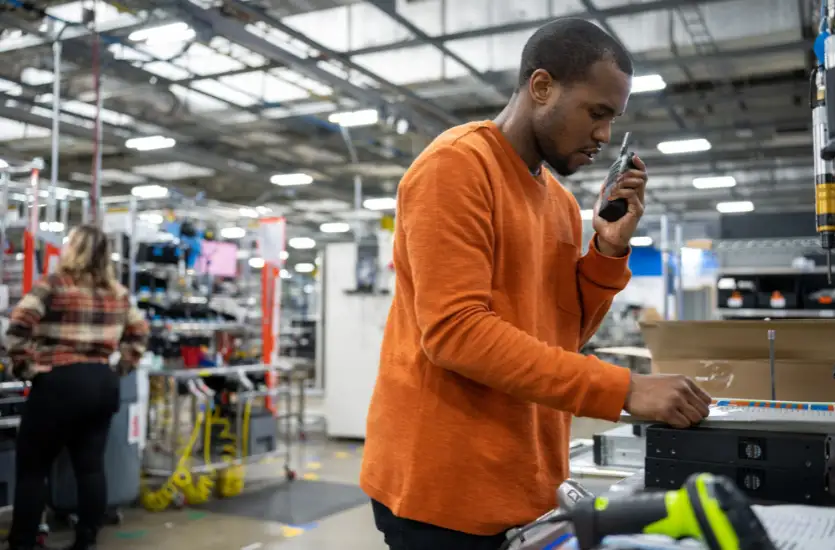
Implementing Motorola’s Ecosystem in Manufacturing
So, just how do you implement an ecosystem like this into an existing manufacturing business? This is where EMCI Wireless can help. As a Motorola solutions channel partner, we do far more than just sell you the technology and send you on your way. We’re there to help you with your communication strategy, ecosystem integration, and everything that comes thereafter.
Consider this hypothetical example, which we designed and built off the mining case study we referred to earlier. A large manufacturing plant faced ongoing challenges with communication breakdowns between departments, especially when teams were spread out across different sections of the facility. These issues led to delays in reporting safety concerns, slowed down equipment repairs, and created inefficiencies in operational coordination. By integrating Motorola’s communication ecosystem through WAVE PTX, the plant was able to connect all employees, from technicians to floor managers, on a single platform.
One immediate improvement was in safety. Workers could now send real-time alerts when issues arose, and supervisors had access to precise location data. This helped reduce the number of safety incidents and improved the overall response time in case of emergencies.
In terms of efficiency, the plant saw significant changes. Communication gaps that once caused delays in maintenance and production were now a thing of the past. Technicians could share video footage of malfunctioning machines with off-site engineers, allowing them to troubleshoot without having to be on-site. This sped up repair times and minimized downtime across production lines.
Lastly, operational continuity was improved. With better communication tools in place, management had greater visibility into daily operations, which helped them make informed decisions faster. And we can be there to help make all this happen for your business, too.
Increasing Management Visibility and Decision-Making
Motorola’s communication ecosystem equips management with real-time data and live updates, offering a clear view of day-to-day operations. With WAVE PTX, senior personnel can remotely monitor key activities, track team locations, and access important information without being physically present on-site. This added visibility allows managers to make timely decisions, address any concerns before they escalate, and keep operations running, even from a distance.
It’s important to note that this isn’t a “big brother” approach. Instead of micromanaging, the system provides necessary oversight for maintaining safety and operational flow. Management isn’t watching every move, but rather receiving key data when something needs attention—whether it’s an emergency alert, equipment failure, or production issue. The goal is not surveillance but rather a tool for better coordination, allowing managers to step in only when required.
EMCI Wireless is Your Partner in Integrating an Advanced Communication Ecosystem
Ready to learn more about how WAVE PTX can improve your manufacturing operations with an advanced Motorola communication ecosystem? Contact us today for a free consultation. We’re here to help you every step of the way.